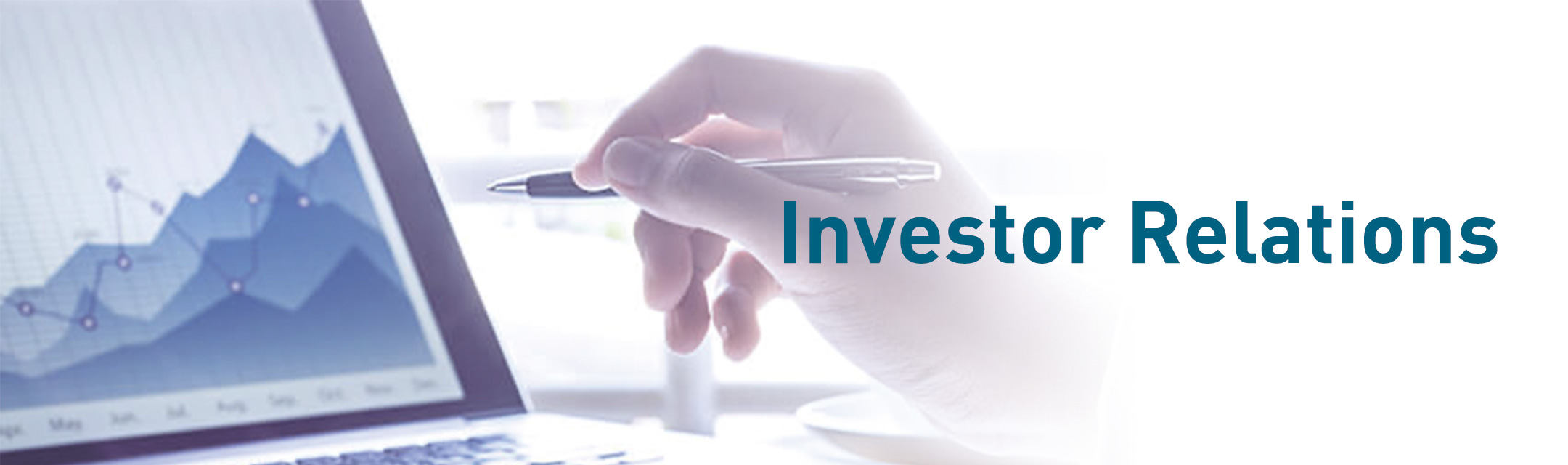
The Nisshin OilliO Group (hereinafter “the Group”) defines uncertainties that will have a negative impact on the achievement of its “Vision 2030,” medium-term management plan “Value Up +,” as well as its business endeavors as “risks,” and carries out risk control efforts to mitigate these risks. Through independent risk management efforts, the goal of the Group is to not only generate stable revenue as a company, but also to further increase and develop its corporate value through fulfilling its social responsibilities.
The content herein highlights the Group’s material risks selected by the Risk Management Committee from the risk matrix.
Risk Matrix (Material risks identified)
Descriptions of material risks incurred by the Group and measures for addressing such risks are as follows. Whereas the following content includes contingencies pertinent to the future, these contingencies have been identified by the Group as having relevancy as of the end of the fiscal year ended March 31, 2024.
In its Oil and Fat business and Processed Food and Materials business, the Group imports all of its raw materials from overseas, including soybeans, canola, and cacao. It is also extending its overseas operations in locations such as Malaysia, elsewhere in Southeast Asia, and in Europe. The Group accordingly assumes the risk of exchange rate volatility particularly associated with raw material costs, sales in foreign currencies, and borrowings in foreign currencies. Such exchange rate volatility could potentially affect its earnings results and financial position.
As for raw materials, in addition to the risk of market volatility with respect to international prices of raw materials, we also assume the risk of volatility in transportation costs and other such expenditures potentially resulting from soaring crude oil prices. Raw material prices could potentially affect the Group’s earnings results and financial position given that they constitute a key component of its cost structure.
The Group addresses such risks by flexibly arranging forward exchange contracts and hedging transactions enlisting futures markets, in accordance with its regulations on handling trading of derivatives and commodity futures. With regard to hedging transactions, we also share and monitor information on a quarterly basis in meetings of the Company’s Executive Board. Furthermore, the Group is taking efforts to curb the impact of cost fluctuations by optimizing its sales prices to align with the cost of raw materials, as well as reducing its manufacturing costs and other expenses.
Sales of the Oil and Fat business are especially prone to changes in product market conditions in Japan and overseas. Domestic selling prices of oils, fats and meal products generally hinge on international market conditions. In addition, trends with respect to product imports from overseas could potentially affect sales prices in Japan. As such, a scenario where such changes arise with respect to market conditions in Japan and overseas could affect the Group’s earnings results and financial position.
The Group strives to sell its products at fair prices that align with costs and the like according to the fluctuations in product market conditions in Japan and overseas. The Group is engaging in efforts to scale its sales of high-added-value products, gradually increasing its percentage of sales of such products. While sometimes time lags may occur from fluctuations in the cost of goods sold and sales prices, the Group strives to reduce the impact of this risk on its performance. The Company’s Executive Board manages the progress of the management plan every month and feeds the results into the implementation of necessary measures.
In addition to the threat of earthquakes and tsunamis, we are well aware that risks involving recent events such as storm and flood damage due to extreme weather have been increasing from one year to the next. Any materialization of such risk could have an impact on key points along the supply chain, particularly if such a scenario were to adversely affect manufacturing equipment, distribution equipment, infrastructure, or employee safety, which in turn could adversely affect the Group’s earnings results and financial position.
The Group adopted a safety confirmation system designed to check on the safety of employees and others in the event of an earthquake, tsunami, or other such disaster. We have also established a business continuity plan (BCP) that we review as necessary to enhance its effectiveness. At the same time, the Group is proceeding with necessary efforts involving the seismic reinforcement of facilities for the safety of its employees, etc., as well as the enhancement of its production system foundations. The Group is also enhancing its earthquake countermeasures in terms of its embankments and its procurement of electrical power.
We also regularly conduct comprehensive disaster readiness drills and provide necessary education, while also taking action that involves addressing the key issue of disaster mitigation, which partially involves reducing the risk of storm and flood damage caused by extreme weather events in recent years.
We research matters involving the risk of damage beyond the scope of such measures on an ongoing basis, with the aim of minimizing potential damage to the extent possible, while also taking out insurance coverage and striving to reduce effects of such scenarios on the Group’s earnings results and financial position.
Growing social concern when it comes to food quality and safety has given rise to the need for more stringent systems of quality control. Accordingly, the Group’s credibility, earnings results, and financial position could be adversely affected should a situation arise involving quality concerns.
The Group has built a strict quality assurance system. The Quality Management Committee, which serves as an advisory body to the Executive Board of the Company, deliberates on and checks the implementation of policies and measures involving quality assurance. Meanwhile, our major plants in Japan have acquired ISO9001 certification (International Organization for Standardization) and FSSC22000 certification (Food Safety System Certification), which serves as an international standard for food safety management. Also, some of our manufacturing processes have acquired GMP certification (Good Manufacturing Practices).
Among the raw materials required for the Group’s products, the Oil and Fat business and Processed Food and Materials business in particular must procure primary raw materials such as soybeans, canola, and cacao, along with oils and fats such as olive oil and palm oil. Accordingly, deterioration of the environment for procuring such raw materials causing an inability to procure sufficient amounts of raw materials or secure raw materials that meet the Group’s requirements for quality and safety could result in tremendous risks to stable product supply, thereby affecting the Group’s credibility, earnings results, and financial position.
The sense of uncertainty over the supply and demand for food supplies due to an increase in the world’s population and abnormal weather, etc., occurring frequently in each region of the globe continues to grow year on year. Meanwhile, political trends in countries where the Group’s raw materials are produced and increasing geopolitical risks and so on also present the risk of raw material supplies becoming unstable. As a result, great care must be paid to this risk.
In order to be able to address changes in the procurement environment of raw materials brought about by factors such as the impact of extreme weather such as droughts, political trends in production countries, and increasing geopolitical risks, the Group strives to ensure stable procurement by diversifying the production countries and suppliers it uses for raw materials. Particularly in circumstances where trends in the procurement environment are difficult to predict, the Group strives to procure with a vision of demand up to the next procurement period to ensure it has inventory.
Moreover, with the aim of procuring safe raw materials, we have been conducting safety assessments involving analysis and on-site visits when purchasing raw materials from new production regions and suppliers. In addition, with respect to raw materials purchased through existing channels, we regularly conduct safety assessments and collect information on their origins, thereby striving to secure safe and reliable raw materials.
Contemporary issues attracting attention include measures to address global warming and marine plastic waste. Accordingly, an inability to address such challenges could adversely affect the Group’s credibility, earnings results, and financial position.
The Group, which positions plant resources at the heart of its business endeavors, believes the preservation of the global environment and its resources is integral to keeping the company in business for years to come, and thus engaged in the following initiatives to achieve a decarbonized and recycling-oriented society.
Addressing climate change
Environmentally conscious efforts
Reduce use of plastic containers and packaging
If the Group or a supplier causes a human rights problem or procures in a way that is problematic in terms of human rights, this could impact the Group’s credibility, earnings results, and financial position.
In fiscal 2023, we created a roadmap for human rights due diligence and established The Nisshin OilliO Group Supplier Guidelines. We also assessed risks related to human rights that may arise in the Group’s operations and conducted a survey of high-priority suppliers.
In fiscal 2024, we will take steps to establish a mechanism and system to promote human rights due diligence in earnest, and also continue with further supplier surveys.
Changes in consumer needs in recent years have been extremely quick and become increasingly diverse, with consumer needs potentially changing before the Group is even aware of them. There is also the possibility that the Group cannot meet the needs even if it is aware of them, which may impact the Group’s earnings results and financial position.
The Group constantly strives to grasp changes in consumer needs as soon as possible, and has, for example, taken the following actions.
In the past several years, the surging price of oils and fats and the ongoing rise in the cost of living have increased consumers’ inclination to use edible oil more carefully. To meet that need, we released Nisshin Canola Oil Halfuse, a product that adds new value in the form of encouraging consumers to use less.
The oxidation of oils and fats is another concern or interest consumers have developed around edible oil of late. Although we focused on developing technology to curb increasing oxidation for many years, we have now combined our technologies to develop a new ultra oxidation barrier manufacturing method. We then used this technology to release Nisshin Healthy Clear, an edible oil that delivers long-lasting freshness even after the bottle is opened.
As an initiative to enhance our customer touchpoints, we launched a website that delivers useful information for commercial customers in restaurants, ready-to-eat meals, and similar business domains.
The Group has been expanding its business not only within Japan but also in Southeast Asia, Europe and elsewhere. The following scenarios pose risks, particularly when it comes to overseas business development.
If these events occur, they may impact the Group’s earnings results and financial position.
To minimize such risks, the Group will endeavor to collect information and respond accurately and promptly within the crisis management structure.
The Group’s earnings results and financial position could be adversely affected amid a potential scenario where key points of the supply chain become subject to the effects of situations that could include the prevalence of communicable diseases, infectious diseases or other such developments; contagion of employees or others; restrictions imposed on business activities including those of outsourcers; or insufficient procurement of raw materials, disrupting the stable supply of products as a result. The Group’s earnings results and financial position could also be adversely affected should product demand become subject to significant volatility.
Based on our experiences from dealing with the COVID-19 pandemic, we revised the functions, roles, personnel structure, and other aspects of our Task Force and brushed up areas of our BCP documents pertaining to infectious diseases.
The Group has established information systems for the purposes of achieving smooth and efficient execution of business operations encompassing production, logistics and sales management, as well as finance and accounting. We also retain important information for business operations along with confidential and personal information gained in the course of doing business. In the event business delays and data breaches associated with potential system disruptions arise due to the likes of major disasters, power outages, computer viruses, or cyberattacks, the Group could lose the credibility of its customers and the market, ultimately impacting the Group's earnings results and financial position.
In order to secure stable operation of the Group’s information systems, improve its credibility, and prevent data breaches, the Group has taken action that includes adopting tool-based security measures, conducting employee education and training, and taking steps to ensure that risks do not materialize. Furthermore, in preparation for security incidents, the Group has put in place manuals and a communication structure for responding to security incidents. The Information Security Committee is regularly furnished with reports on information security measures, which it evaluates and reviews.
If large-scale accidents such as fires or explosions occur, they will disrupt the stable supply of products and could impact the Group’s credibility, earnings results, and financial position.
In addition to appointing an officer in charge of safety and disaster prevention that are responsible for overseeing company-wide safety and disaster-prevention management, we have set up a company-wide disaster prevention system, focused on safety and disaster-prevention meetings, as well as a workplace disaster-prevention system. Furthermore, in addition to stipulating a system in case of emergencies, we regularly hold general disaster drills and educational training, striving to prevent accidents as well as prepare itself in the unlikely event that one might occur.
The Group strives to reduce the impact of this risk on its earnings results and financial position by carrying out the aforementioned efforts and taking out insurance coverage.
We strive to ensure our access to requisite logistical capabilities at appropriate cost so that we are able to deliver products to our customers in line with their requests. However, in the event the Group cannot do this, the supply of products to customers will be delayed, and it could impact the Group’s earnings results and financial position.
In Japan, we face concerns that demand may come to exceed supply in the realm of logistics amid the possibility of decreasing freight capacity domestically going forward, given the nation’s prevailing shortage of truck and lorry drivers along with its aging population. Moreover, there is the risk that it may no longer be possible to deliver products to customers as a result of slow progress achieved with respect to making improvements that address issues involving logistics, particularly in terms of long waiting times such that are typical in the food industry as well as tasks incidental to making deliveries.
We also face concerns regarding the possibility of logistics demand exceeding supply similarly given a shortage of seafarers who operate coastal trading vessels and an aging population.
When it comes to products in the household-use and commercial-use domains of the Oil and Fat business, the Group strives to reduce such risks by taking steps that include reassessing delivery lead times, overhauling or expanding inventory facilities, securing alternative means of transportation such as rail or vessels, as well as promoting sustainable logistics initiatives and optimizing shipping fees. In fiscal 2023, we set new CSV goals for increasing the co-distribution rate and reducing truck driver time spent at Company plants to establish a more competitive and sustainable logistics system.
We will also further promote shipping handled jointly through a logistics company funded by Ajinomoto, Kagome, The Nisshin OilliO Group, Nisshin Foods, and House Foods Group, and initiatives to improve our logistics.
Going forward, the Group will also continue to examine initiatives to optimize the entire supply chain through the use of digital technologies, in pursuit of achieving “local production for local consumption,” whereby the Group delivers products that have been manufactured at factories situated in closer proximity to the site of consumption.
Professional talent equipped with diverse values and expertise is a must in achieving the vision set forth under The Nisshin OilliO Group Vision 2030. Meanwhile, a shortage of such talent would result in diminished competitiveness.
On the other hand, when it comes to the notion of consistently providing safe and reliable products, we are particularly aware that a prospective shortage of talent tasked with activities involving production and distribution sites constitutes a major risk in terms of our business continuity.
In addition, personal health is the most important factor for each and every employee to achieve personal and professional fulfillment, while also persistently demonstrating their potential enthusiastically within the Group. Our exposure to employee health risk could adversely affect productivity and other aspects of operations.
The Group is taking further action to secure and reinforce requisite professional talent by focusing efforts on creating a vibrant organization that gives rise to innovation. This involves valuing employee diversity, increasing investment in human resource development programs that enable each and every individual to grow, recruiting talent from outside the Group as necessary, empowering female employees, and promoting health management.
The Group’s efforts to consistently provide safe and reliable products involve taking steps to secure and retain professional talent in part through ongoing recruitment and training, actively utilizing remote work, and optimizing working conditions. The Group also streamlines operations and achieves labor savings by enlisting IoT, AI, and other such technologies.
Having established a framework for promoting health management, to which top management holds the ultimate authority, the Group engages in various health management initiatives for the purposes of achieving better physical and mental health for employees, job satisfaction, and productivity gains.